Last weekend, I replaced the CV joint boots
on the rear axle and thought I'd share the experience with pics.
I
had never done this before so decided to go all the way and take the
joints apart and inspect and get a little experience. Besides, I had never
actually seen a CV joint before and had to know what was in
there!
Leave the car on the ground, weight on wheels, and go after
the wheel nuts. I applied the parking brake and I used a 1/2" breaker bar
and 1 1/4" 6-point socket to loosen. Ended up putting my foot on the
handle and applying most of my weight (but not all) and it came loose with
no fuss. I went ahead and took the nut and washer off. I would recommend
using an impact socket and an extension bar on the breaker bar handle to
make it easier. Then jack the car up at the rear for the rest of the job.
It was not necessary take the wheels off for the job, so I left them
on.
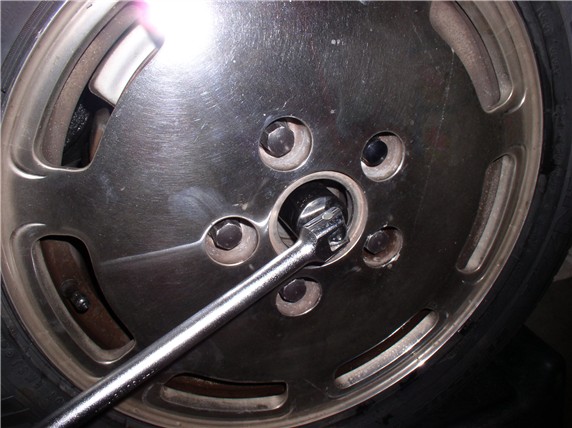
Next, I detached the exhaust at the back of the cat -
13mm nuts. You'll need to counterhold the bolt end. I supported the cat
with a floor jack. I used WD-40 on the nuts to ease them off. My brain
said, "use a small amount", my finger didn't listen!
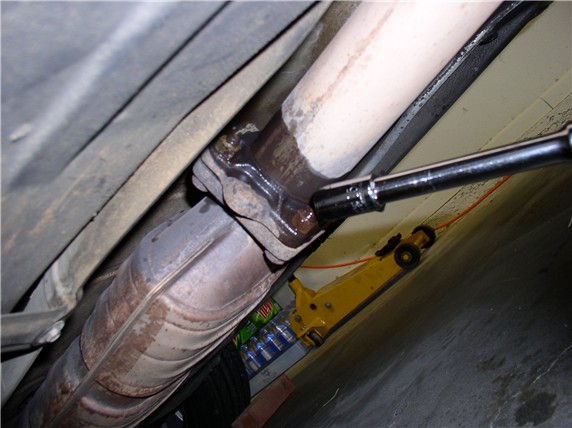
Then came the mid-exhaust hanger - 13mm nuts. Counterhold
the bolt end. Simply detached at the bracket bolts.
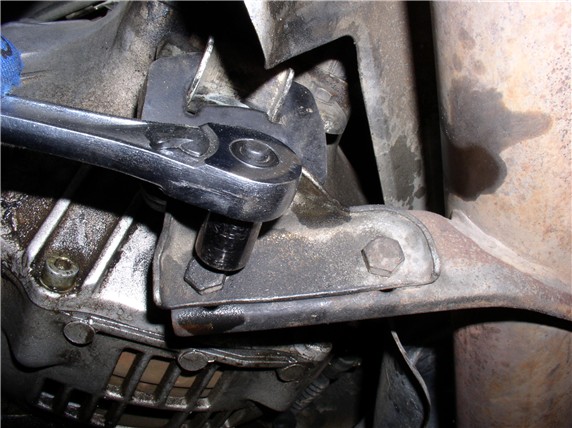
At this point I simply let the exhaust rest on the
ground. It allowed enough room to remove the driver side axle.
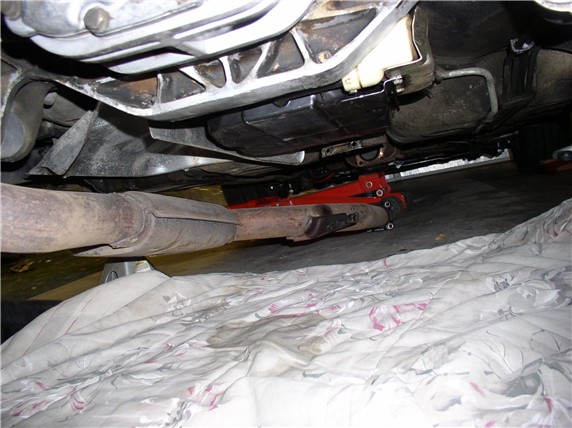
Here's the inner boot that was torn. I could see no signs
of lube flung everywhere and in fact it looked like it had been torn for
some time. Lube was being flung at the outer boot (same axle) and seemed
to be coming from the small end of the boot seal around the axle.
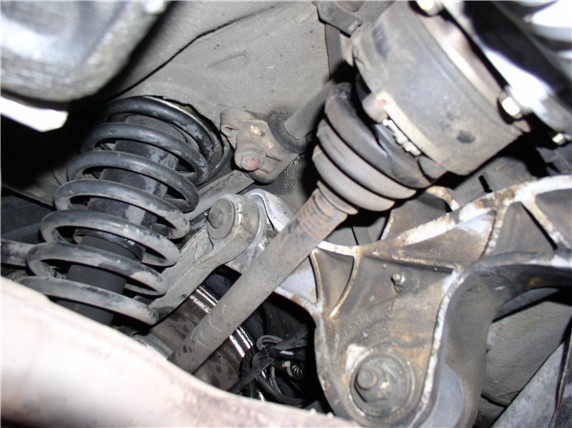
To take off the Allen bolts, use an 8mm
Allen socket.
There are six bolts per axle. With the parking brake set, I did 2 at a
time on each axle then released the brake and rotated the tires so the
next 2 were accessible. Set the brake and loosen. Repeat until all 6 are
out. One thing I had to keep in mind was making sure I had good contact
with the Allen socket in the bolt head. With the boot a little in the way
there, and not rotating the tire to get a good position, I could see how
easy it would be to get the Allen in slightly crooked and strip the bolt
out. So be careful and take your time.
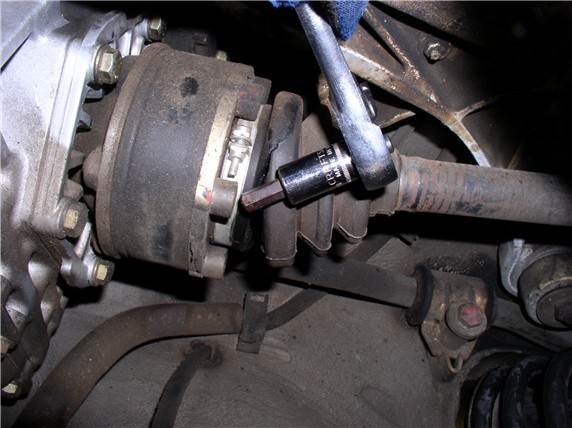
Once the bolts were out, I simply rested the axle on the
suspension tubes while I went around to the outside of the wheels to push
the axle out.
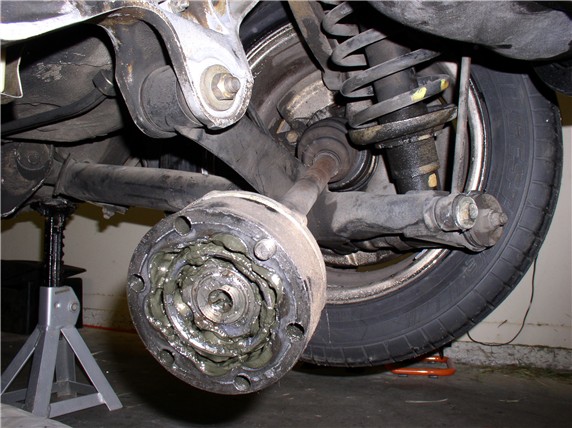
I fashioned a wooden dowel to tap the axle out. Used a
wooden closet rod laying around and shaped the end down with a Dremel to a
dimension slightly smaller than the axle so it would fit into the hub
spline and fully push the axle out. A few taps with the hammer and they
come right out.
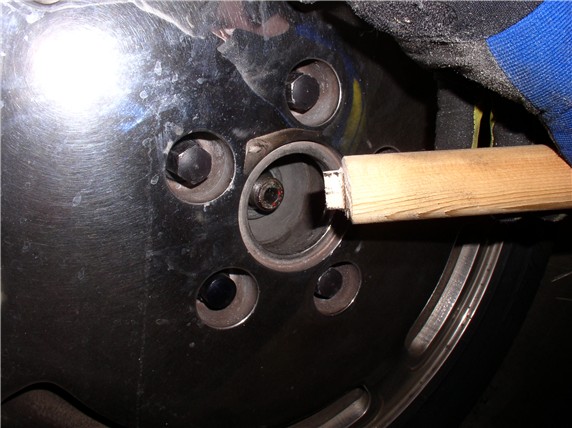
Got back under the car and easily maneuvered the axle
out.
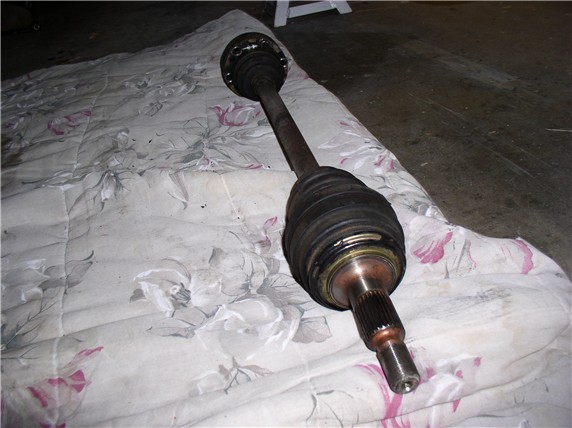
Here's a pic of the inside wheel the axle came out
of...
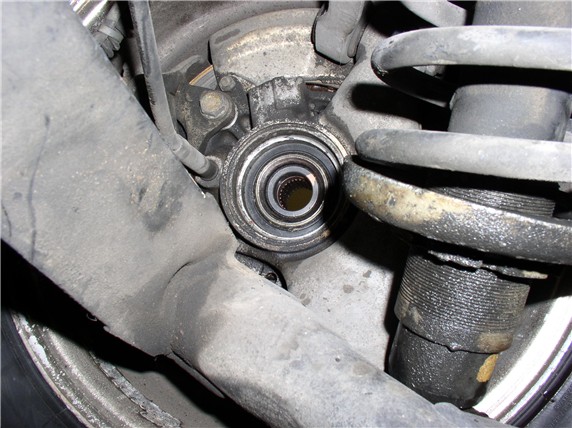
After the axle is out, I put it on the bench and removed
the clamps on both inner and outer boots. I then pulled the boot off the
flange and simply used a utility knife to cut/saw though the boot
carefully.
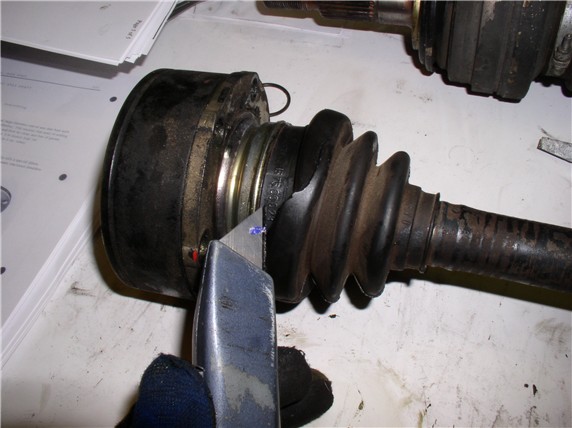
With the boots off, the joints were ready for an initial
cleaning - lots of grease, couldn't see anything.
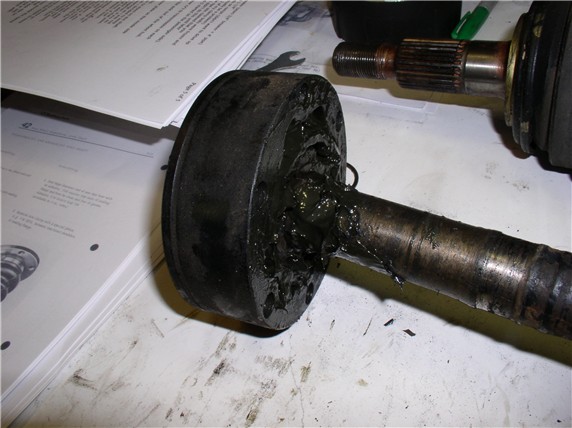
I wiped a lot of the grease off with a rag first, then I
used odorless mineral spirits to clean off most of the grease. To clean
the outers (since the joint is welded on), I used mineral spirits in a
good spray bottle and sprayed jets into the outer joint. The dissolved
grease drained out the bottom of the shaft. Took about 20 minutes to get
one outer joint good and clean this way. I went through almost a gallon of
mineral spirits.
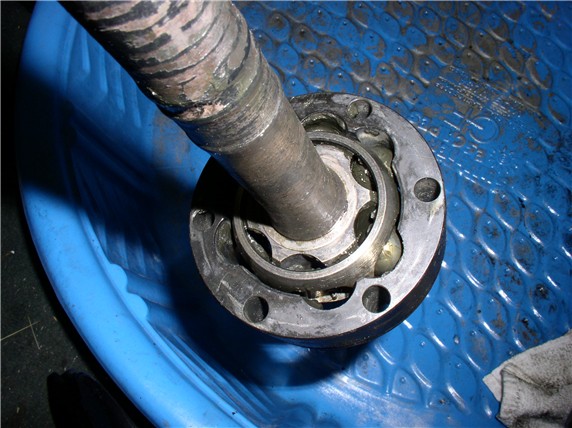
Once the grease is cleaned off enough to see
things. I took off the circlip holding the cv joint on the axle. I first
used snap ring pliers but it took a bit of work to get one off. So I
bought some pliers made for the job and it worked much better. A picture
of the correct pliers comes later. I also made note at this point any
distinguishing marks to identify which way the bearing hub, cage and outer
collar were oriented for reassembly. For example, the outer collar has a
groove in the outer surface near the end that mates to the transmission.
The bearing hub has a groove in the surface that faces the transmission
(see picture - close to circlip). Even the cages had a slight difference
in top and bottom edges. Around the rim on the top edge of the cage, the
"flat" is narrower than on the bottom rim of the cage - it's a slight
difference.
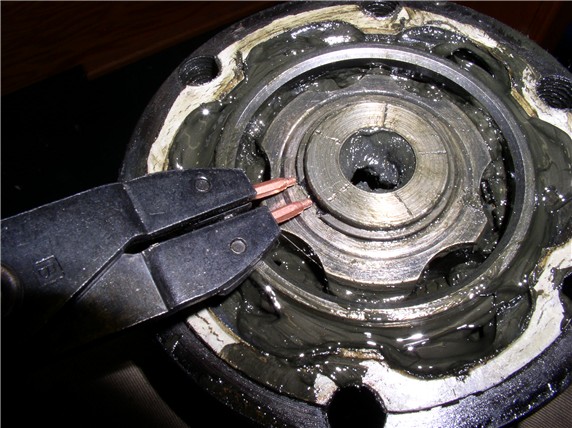
After the circlip is removed, I took the axles to the
auto hobby shop to borrow their hydraulic press to press the axle out of
the cv joint. On the way to borrow the press, the wrapped axles broke free
from the blanket I wrapped them in and before I knew what happened, I
began to hear all kinds of metal parts klinking together in the back of my
car. The bearings had come out! Not what I planned. The WSM says to keep
the cv joints together and not mix them. The bearings belong to a
tolerance group. However I could see no distinguishing marks to match the
bearings to the cv joint. The rest of the joints I was able to keep
together (bearing hub, cage and outer collar). When I got the shop, the
axles pressed out of the joint easily. I need to get a press for home --
think I will take a look at what HF has.
When I got back home, I
cleaned each bearing, cage, bearing hub, and outer collar with a rag and
inspected them. Of course, I have no idea what looks good or what looks
bad. So I posted some pics on rennlist and the opinions were they look
fine. Here's one of the bearings:
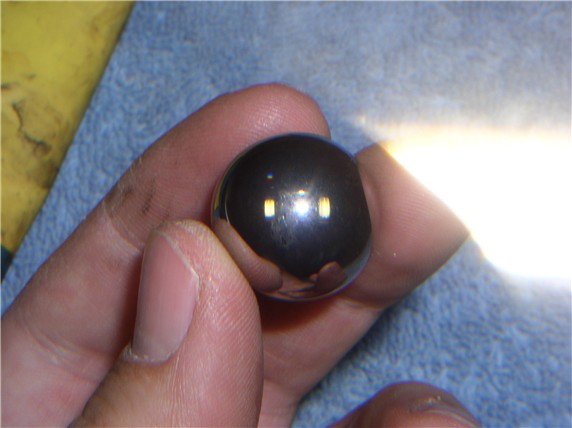
Here's one of the cages. You can see where the bearings
contact the cage but the wearing is very light.
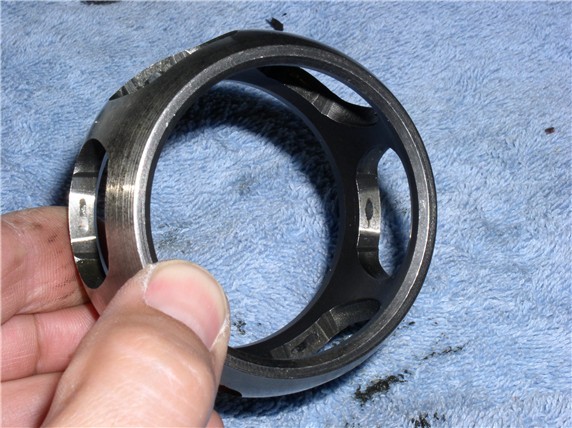
On this cage, there was some imprints on the outside of
the cage but not serious enough to warrant replacement.
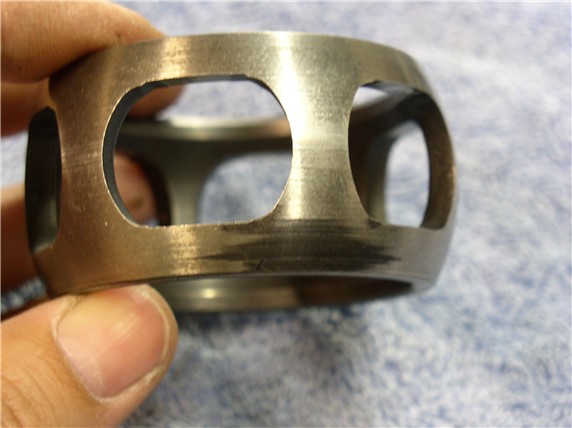
Here's the hub. You can see where the bearing contacts
are. Running my finger over the shiny spots, there was imperceptible wear
at these places so It was also good to go back in.
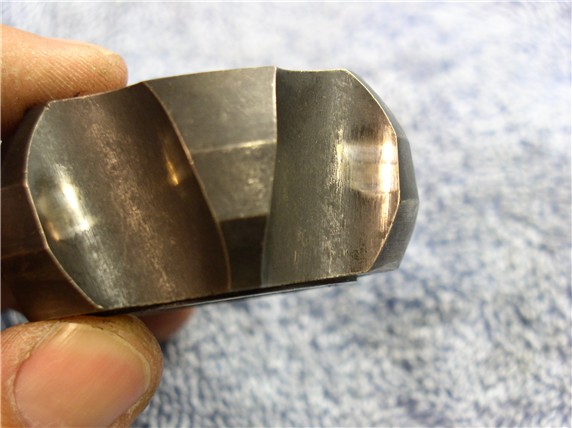
I began reassembly of the joint by placing the bearing
hub in the cage. I made sure the hub and cage were matched same as when I
took them apart (i.e., groove in hub on top, cage top matched). Cage slots
can be matched up with any hub bearing slot - makes no difference
according to the WSM.
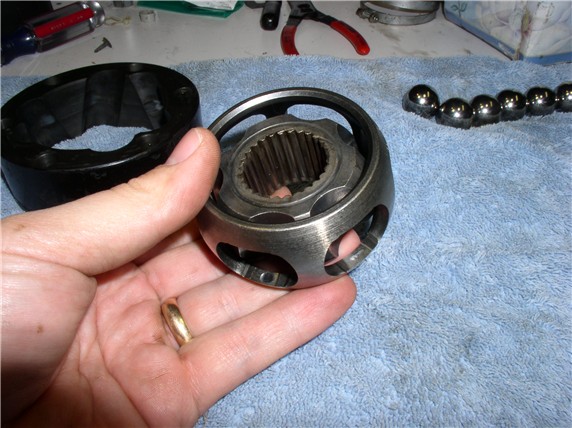
Then place the 6 bearings in (from the outside of the
cage). Since all my bearing were mixed up. I picked any 6.
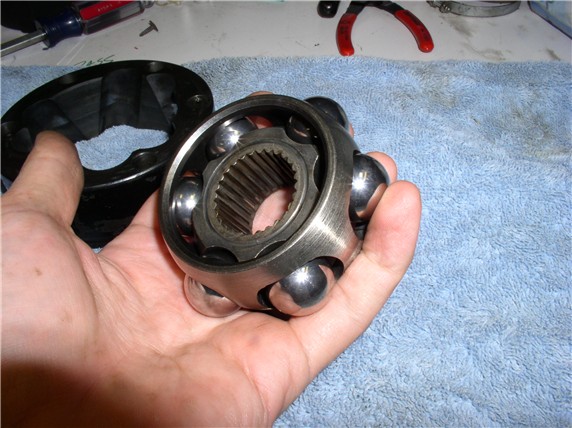
The tricky part is placing the hub/cage/bearings into the
outer collar. Notice the groove on the outer surface of the collar - it's
near the end that will face the transmission. I slid the assembly into the
collar sideways then rotate the bearing assembly around (swing it into the
collar). If a bearing falls out, it's can be re-inserted after you get it
the rest of it together. The WSM has a picture of this. You have to match
the narrow surface areas with the wide surface areas of the collar to get
it right. Notice at the 12 o'clock position of the outer collar (where the
Allen bolt goes). Right below that is the narrow surface of the collar -
notice the bearing hub at the same location - its wide. Also, If the joint
is locked when you press in the hub assembly, you missed it. That's what I
did first time. Then I took it back out, rotated the bearing assembly
right one bearing and put it in again and presto! It worked. The inner
assembly should move freely.
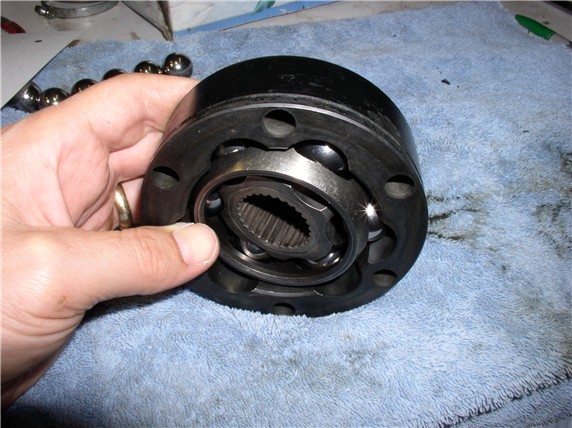
Here's the two joints assembled...notice the wide is
matched to narrow on the inner hub and outer collar.
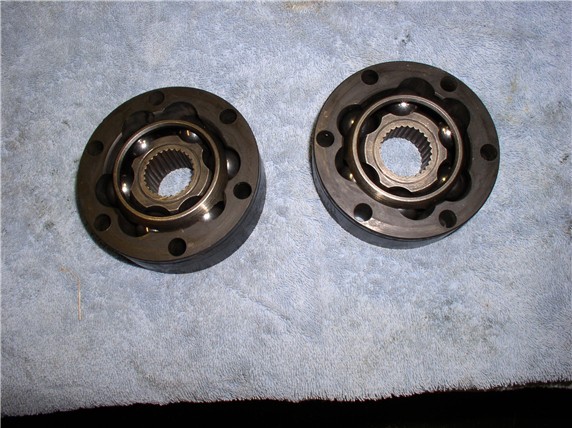
I purchased the boot kit from 928 Intl. One kit came with
one boot, one large clamp, one circlip, one gasket/seal and 2 tubes of
grease. Both tubes of grease go into one joint.
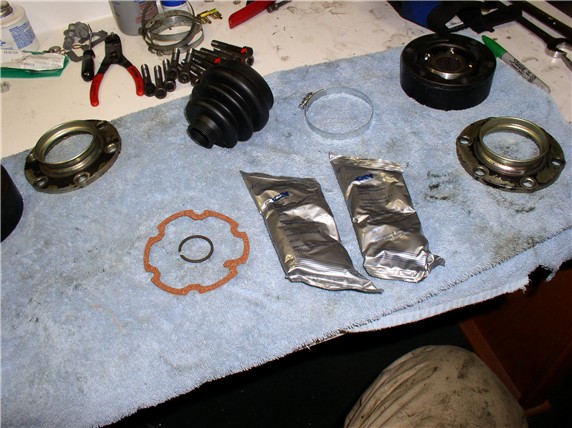
Next it came time to put the 2 tubes of grease in the
outer joint first. Hold the axle vertical with the outer joint down near
the ground. Press the axle down to create more space to squirt the tubes
of grease in until its full. Smear it around so the grease is level with
the boot flange.
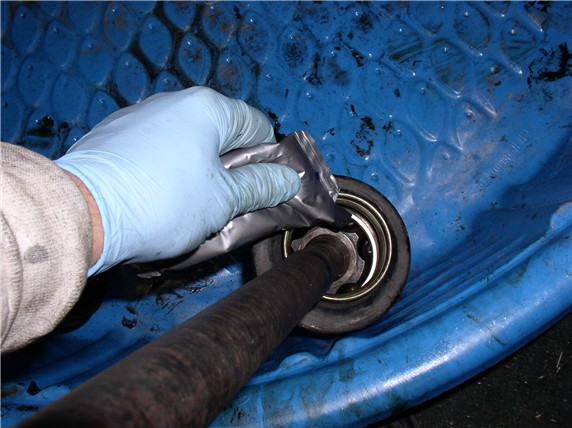
This next trick I learned reading the CV boot replacement
tips I found on Nichols (I believe). You suck the grease into the joint.
Place one hand on the bottom of the axle shaft and place your finger over
the end of the axle to plug the hole. With the other hand at the other end
of the axle, place your thumb over the end of the axle to plug the other
hole. Then pull on both ends of the axle (in opposite directions). This
sucks the grease into the joint. If you've sealed both ends of the axle
well, it will be difficult to pull on both ends of the axle. When you've
pulled the joint all the way up, remove one of your fingers and push it
back down again, plug the holes and pull on the ends of the axle again.
Repeat several times and you will see the grease disappear into the joint.
I did this until both packages of gease had been sucked into the joint.
Here's a pic -- wish I had a 3rd hand to take the picture!
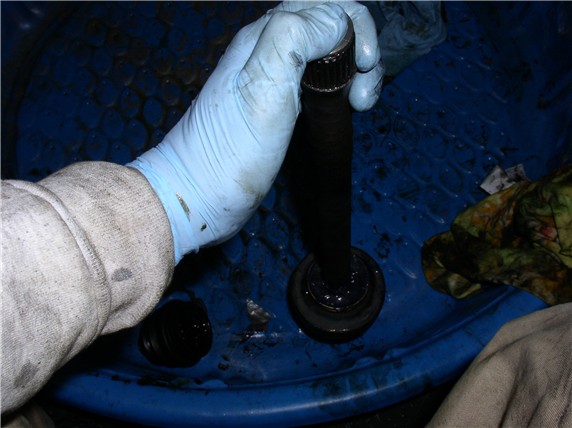
After the grease is in the outer joint, I cleaned off the
excess from around the boot flange.
Next I put
the boot on the outer joint. I simply slid the boot over the axle end and
down the axle. Then pulled the boot over the flange where it locks into
place.
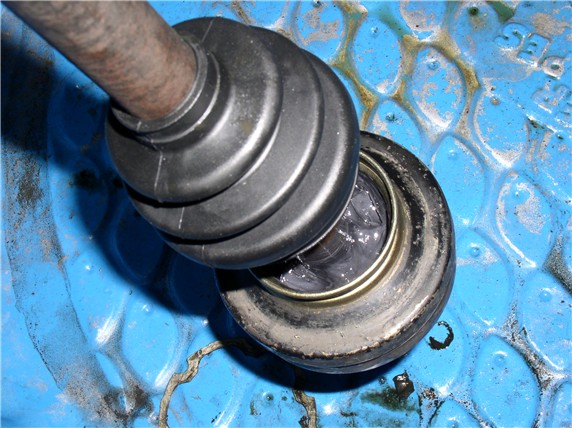
Then put the clamp on....
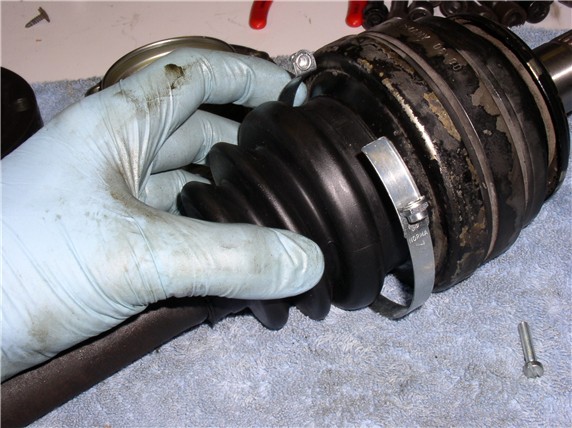
Next was the inner boot. First attached the large opening
of the boot on the flange. This was easier than the outer joint because I
could get at the inside of the boot through the flange to help it
along.
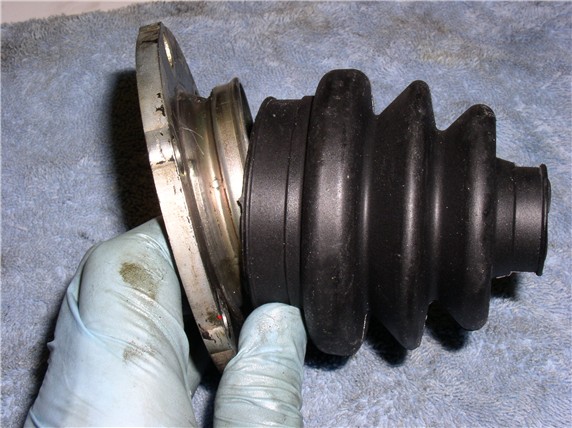
When putting on the clamp, make sure you position the
clamp screw between the bolt holes so it doesn't interfere with the
bolts.
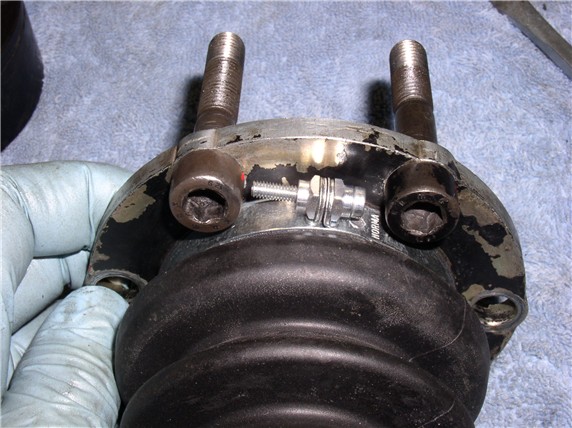
Next, put the inner boot on the axle. A little more
difficult to put on small end first.
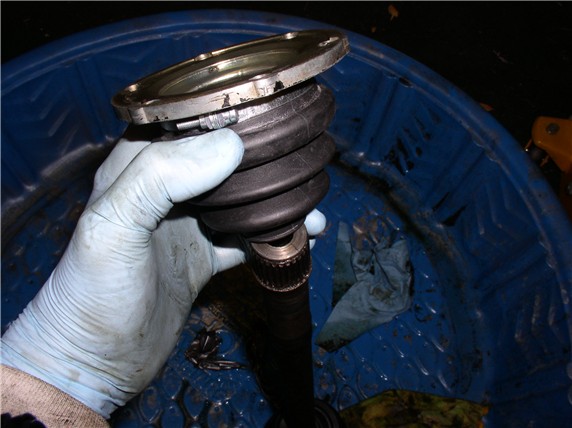
When reading through the Nichols CV Boot tips, I ran
across a tip that someone used a piece of tin cut down and rolled inside
the boot to help get it slid on. This was a great idea! But I couldn't
find any tin around, so I used the next best thing that was handy - a
Ziplock Baggie! Of course! I rolled the baggie around the axle - Ziplock
end toward the outer CV joint (this gives you something to grip onto when
pulling the boot on).
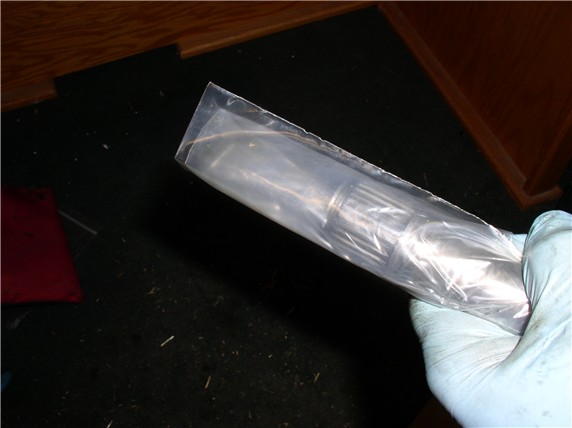
Next, thread the end of the baggie through the small boot
hole and push the small end of the boot onto the axle shaft. You don't
have to push it on very far, just enough to get it on the very end of the
axle.
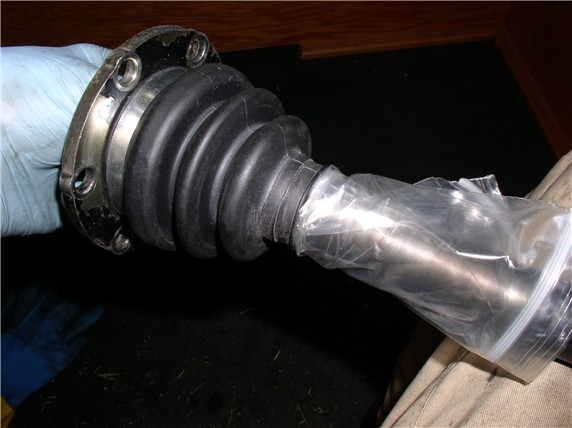
Then push the boot from the top while pulling on the
Ziplock end at the bottom and the boot slides over the the axle shaft.
Works slicker than snot, literally!
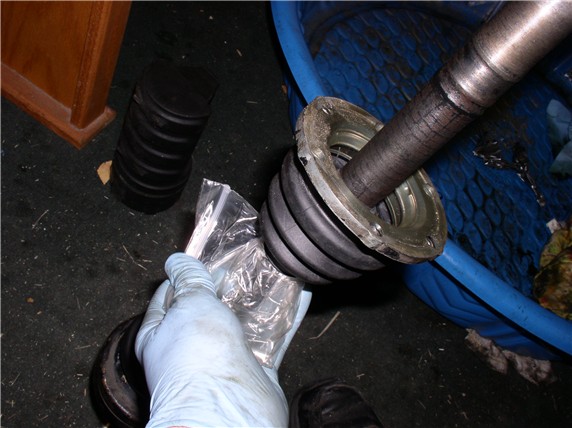
I pulled the boot all the way down the shaft near the
outer cv joint out of the way then simply pulled the baggie out. Next, I
put the flange gasket on - adhesive side toward the flange but didn't
remove the adhease strip yet. I wanted to pack the joint with grease first
then (if I didn't make a mess), attached the gasket to the flange.
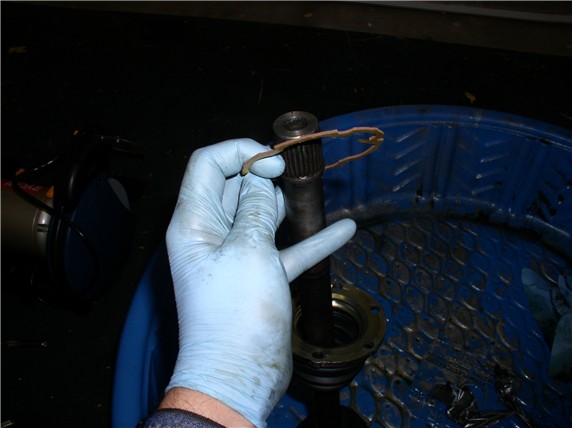
Next, I installed the inner CV joint onto the axle. I
placed the the joint on the shaft and lined up the splines and pressed it
on by hand just to get it started. I made sure it was facing the right
direction (i.e., the groove on the outer collar near the end that's facing
the transmission).
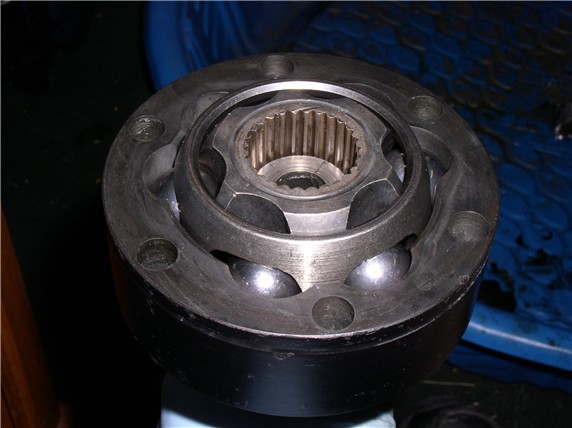
Since I didn't have the hydraulic press, I used the 1
1/4" socket to tap the joint on. Center the socket on the joint then using
one hand, hold the axle shaft off the ground and use the other hand to tap
the socket to push the joint onto the shaft. I gave it 5 or 6 medium-sized
taps and it was on and seated. The mass of the axle and joints provides a
good counter force to the hammer blows so it's not difficult to hold onto
the shaft while tapping the joint on. I didn't want to tap the joint on
while the other end of the axle was on the ground because the outer joint
would be absorbing the hammer blows and THAT didn't sound good.
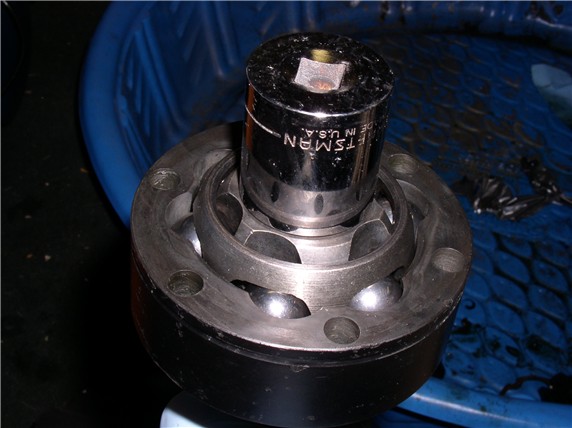
When the joint is fully seated on the axle, the circlip
ring slot on the very end of the axle shaft should be visible.
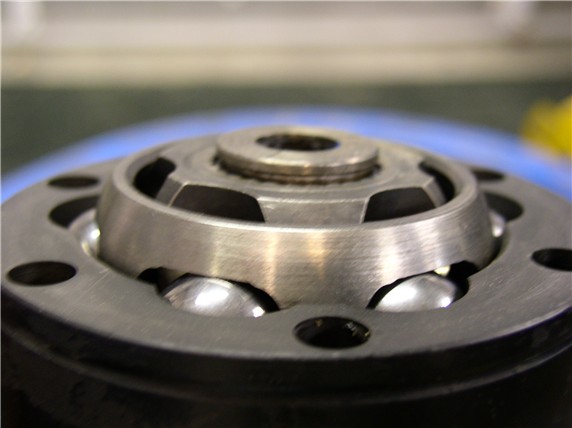
Next, attach the circlip. Here's the pliers I bought to
work with these circlips, much better than trying to use the snap ring
pliers!
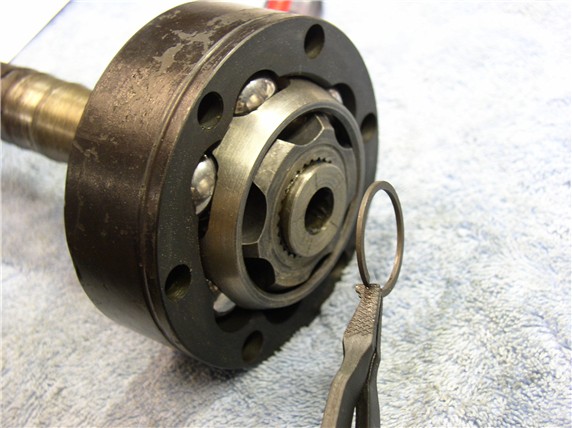
Next, I packed the inner joint with
grease.
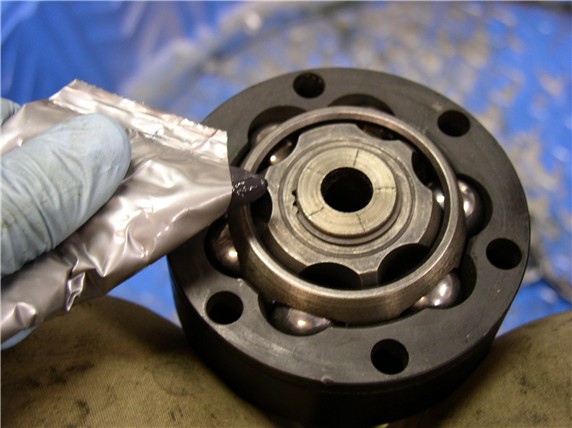
It seemed the best way to pack it in was to press the
grease into the nooks and crannies with my finger and rotate the joint at
the same time. I couldn't quite get 2 packs of lube in without it
producing a mound of grease on each end - ended up using 1 and 3/4 tubes.
After packing it in, wipe off the excess grease from the mating surfaces
of the CV joint. I used one of the Allen bolts to push out any grease that
got into the bolt holes - not shown in this picture.
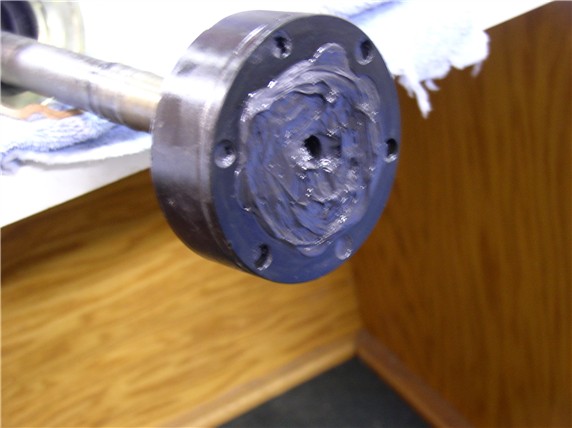
Next, I cleaned the flange surface with brake parts
cleaner to get a grease-free seal for the gasket adhesive. I sprayed the
brake cleaner on a rag then wiped the surface with the rag. I also did the
same to the transmission side flange before adhering the gasket
there.
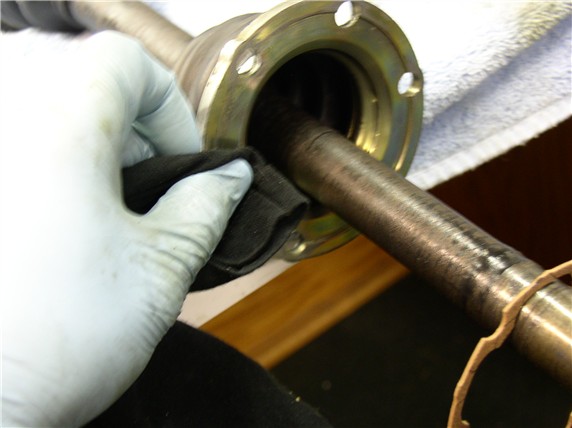
Attach the gasket...
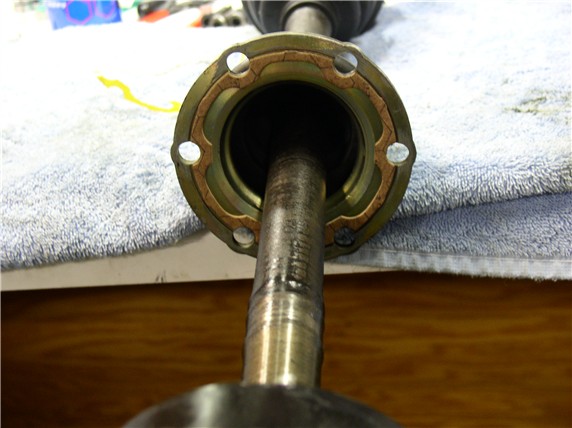
Then I inserted the bolts before sliding the boot down to
the joint so it would be easier to line up the bolt holes in the flange
with the holes in the joint.
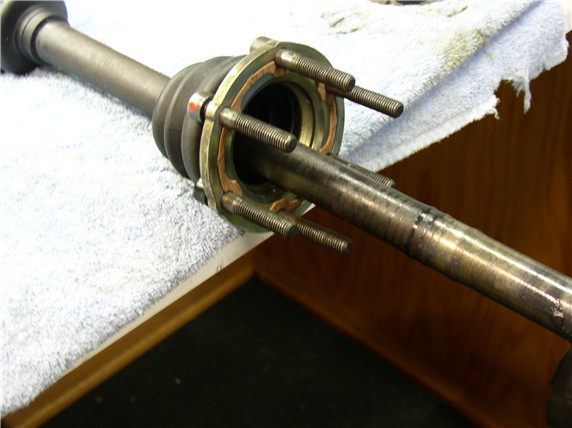
Then slide the boot down into place so the threads are
protruding out the other side of the joint.
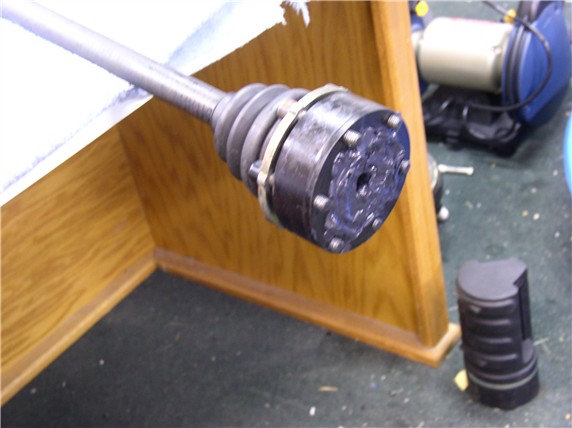
Next, the WSM says to put Optimoly HT, the copper
anti-seize, on the axle splines and wheel nut threads.
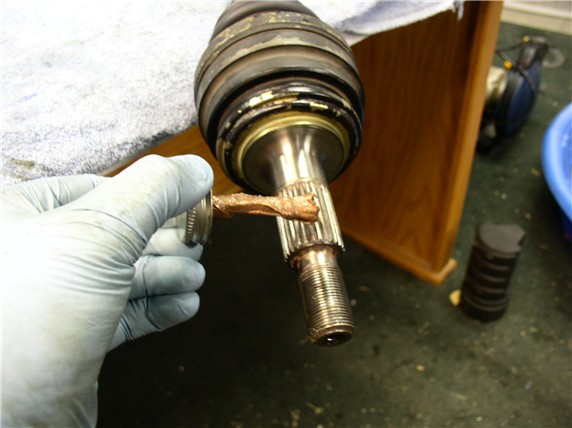
All anti-seized up and ready to go in...
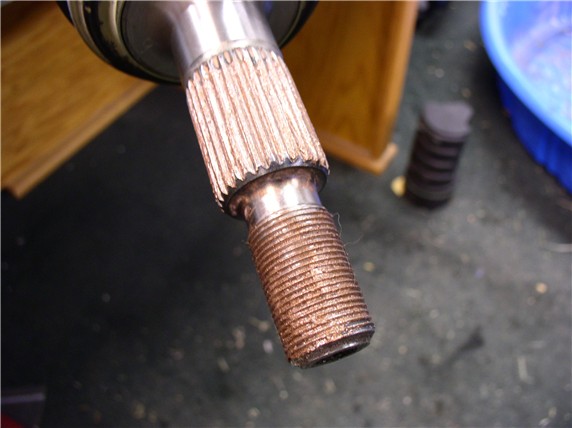
Make sure the flange at the
transmission is grease free
before placing the gasket on. I used brake cleaner on a rag and wiped it
down.
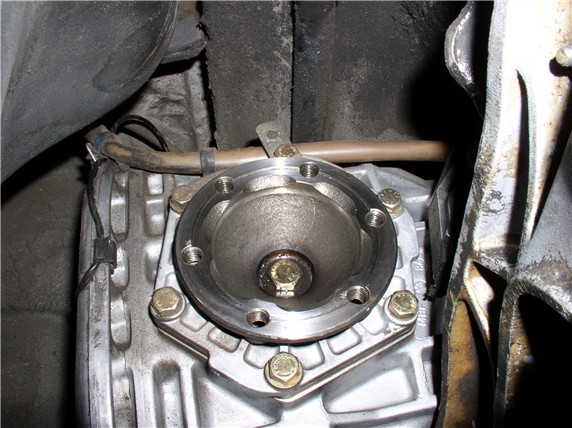
Then attached the adhesive side of the gasket on the
flange.
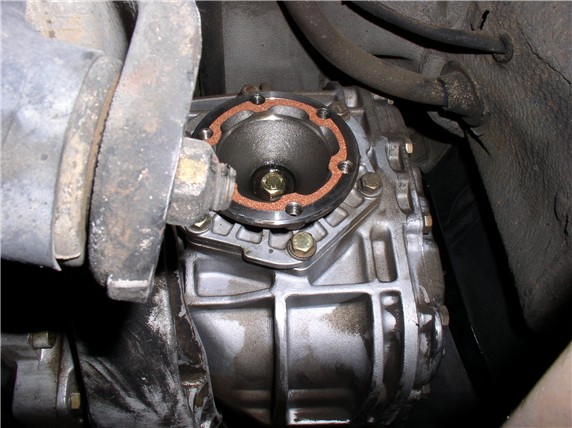
Next, came putting the
outer end of the axle back into the wheel. Simply maneuver the axle into
place and guide the splined end into the hub splines with your fingers.
When the splines were lined up, it slide right in - no force
required.
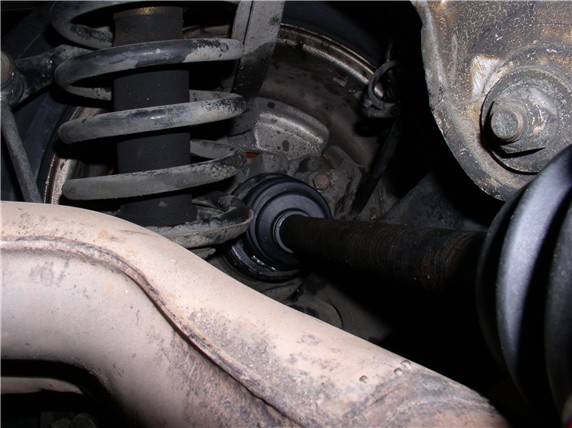
Then I put blue thread locker on the allen bolt threads
before putting them back in.
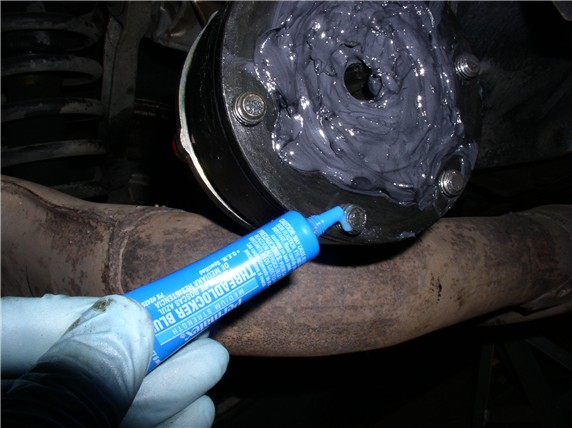
Next, place the inner joint up near the transmission and
line up the bolts with the holes. To line them on the first axle, you can
turn the flange on the transmission to line things up. For the second axle,
it won't be that easy. So I made sure the parking brake was off and I
could turn the wheel to line up the bolt holes with the transmission
flange. Once I got a couple of the "accessible" Allen bolts started, I
simply snugged them down but didn't torque them yet. I rotated the
assembly around to get access to the Allen bolts - snugging all the bolts
down. Then I set the parking brake and torqued 2 bolts at a time - making
sure the Allen socket was fully seated in the bolt head. Torqued to
60ftlb.
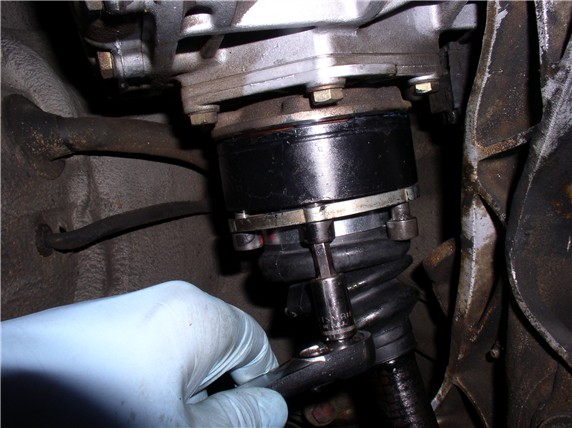
Lastly, I put the wheel nut and washer back on and
torqued them down as well. Unfortunately, my torque wrench only goes up to
250ftlb and I needed about 340. So I tightened them down to 250ftlb and
I'll drive to a local shop that has a larger torque wrench and tighten
down the rest of the way.
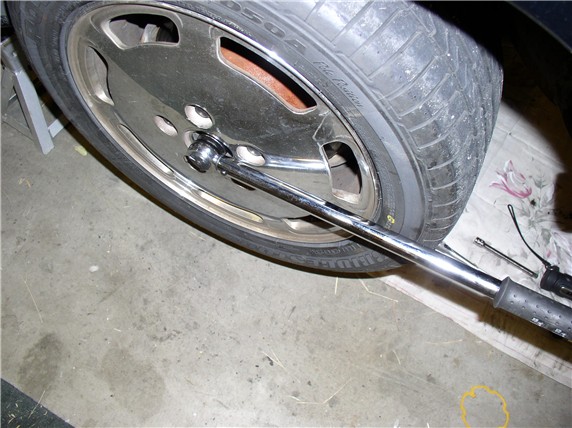
The rest of the job is to put the exhaust back in place,
set the car back on the ground, done. Ours is still on the jack stands
because I'm also repairing transmission fluid leaks while the car is in the
air. Replacing the pan gasket, reservoir o-ring, and intake and return
hoses.
THANKS for reading! Feel free to add comments on
other/better methods - I'm always looking for better/easier ways of doing
things.